Dagelijkse besteldatum om 14.00 uur
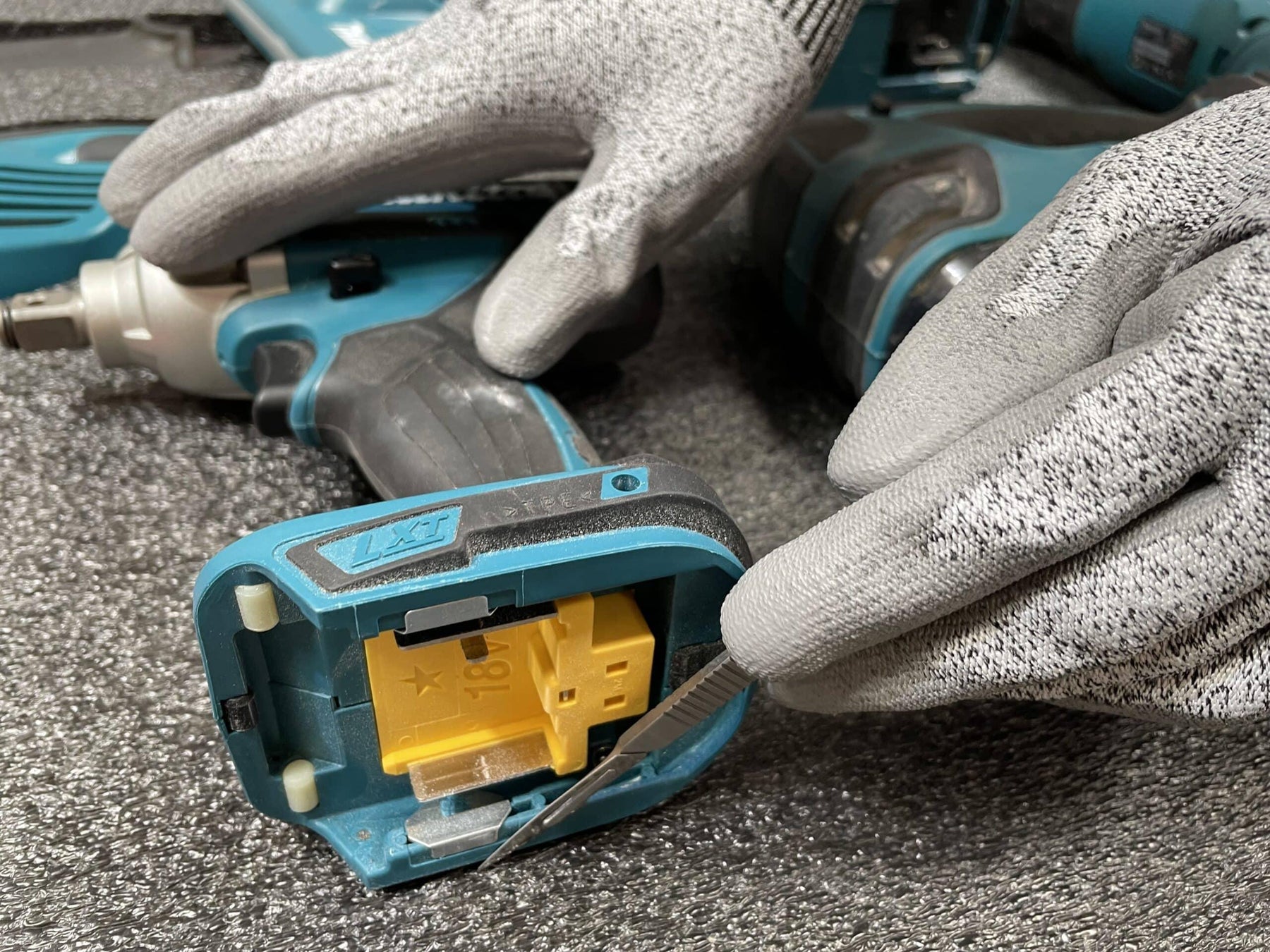
Een gids voor Shadowfoaming
We wilden een lijst samenstellen met de beste hints en tips die we kunnen bieden als het gaat om het verkrijgen van optimale resultaten bij het werken met Shadow Foam. Shadowfoaming is een relatief eenvoudig proces, maar er zijn duidelijke tips die u kunt gebruiken om de beste afwerking van uw werk te krijgen. We hopen dat deze handleiding helpt.
Welke schuimdiepte?

De schuimdiepte is afhankelijk van een aantal factoren: wat uw container is en wat u erin bewaart. Zoals u weet bieden wij 3 schuimdieptes aan , 30 mm, 50 mm en 70 mm. Meestal is voor kleiner, lichter gereedschap, handgereedschap enz. de diepte van 30 mm perfect geschikt. Maar als je grotere, zwaardere items hebt, wil je misschien iets diepers overwegen. Bovendien is het mogelijk om het schuim in laagjes op te stapelen als je het nodig hebt om iets bijzonder groots op te bergen.

Als algemene vuistregel kun je proberen een basis van ongeveer 10 mm aan de onderkant van het schuim te behouden. Dus voor de 30 mm kun je inkorten tot 20 mm, en 50 mm tot 40 mm. En voor de 70 mm kunt u inkorten tot ongeveer 60 mm. Kijk dus eens wat je in het schuim opbergt en op basis daarvan kun je bepalen welke diepte schuim je nodig hebt.
Probeer het voordat je koopt
Als je onze toolbox organizers nog nooit eerder hebt gezien of gebruikt, raden we je aan om het eerst eens te proberen. U kunt een proefpakket bestellen , vaak heeft u deze de volgende dag al in huis. Het kost £ 5 (inclusief gratis verzending in het VK) en je krijgt zelfs een voucher van £ 5 voor je eerste bestelling, dus het hoeft je niets te kosten.
Planning
We zeggen altijd dat dit een van de langste onderdelen van het proces bij Shadowfoaming zou moeten zijn. Neem de tijd om na te denken over de beste lay-out voor u. Jij bent degene die het gebruikt, dus het moet worden afgestemd op jouw behoeften. Je wilt dus natuurlijk dat het er goed uitziet en esthetiek is belangrijk. Maar denk ook na over welke items u regelmatiger nodig heeft.
Andere factoren waarmee u rekening moet houden, zijn de ruimtebesparing als u veel uitrusting heeft... misschien heeft u een aantal items die u in een dubbele laag wilt hebben? Of omgekeerd: toekomstbestendig maken als u denkt dat u in de toekomst mogelijk extra gereedschappen of apparatuur gaat toevoegen.

Als je eenmaal een lay-out hebt waar je tevreden mee bent, maak er dan een foto van voordat je begint met knippen, zodat je tijdens het werken niet vergeet hoe je het wilde hebben.
Apparatuur
Alsjeblieft, alsjeblieft, we kunnen dit niet genoeg benadrukken. Wanneer u met messen werkt om uw opslag te produceren, zoals hier moet, doe dit dan veilig. We hebben een hele reeks producten die zijn ontworpen om u te helpen nauwkeurig en veilig te werken en die speciaal zijn samengesteld met Shadowfoaming in gedachten. Denk er dus over na of u alles heeft wat u nodig heeft, en zo niet, breng dan een bezoek aan onze Extras -winkel.
Als absoluut minimum heb je een aantal sterke snijhandschoenen nodig – die kun je krijgen in onze volledige snijsets . Dan iets om het schuim mee te snijden. Nu weten we dat mensen allerlei geweldige, scherpe messen hebben, maar we raden aan om waar mogelijk een scalpel te gebruiken, zodat je een echt nauwsluitend profiel tegen de voorwerpen kunt snijden zonder enige vervorming door de grotere handgrepen. Je kunt deze krijgen in onze basissnijpakketten, volledige snijsets en je kunt zelfs extra mesjes krijgen als je dat nodig hebt. Een mooie aanvulling op je kit is onze Fantastic Elastic Glue . Als Shadowfoaming nieuw voor je is, dan is dit een must-have, omdat eventuele reparaties netjes en op zo'n manier kunnen worden uitgevoerd dat je met het schuim kunt blijven werken.

Maar voor alles wat u nodig heeft, van snijmatten tot radiusmeters, is het zeker de moeite waard om de sectie Extra's te bezoeken voordat u met uw schuim afrekent om te zien wat er nog meer van pas kan komen.
De pasvorm
Als je een van onze op maat gemaakte inzetstukken hebt gekocht, heb je een winnaar gevonden en kun je dit stukje overslaan!
Maar als u uw eigen inzetstuk wilt maken voor elke container, tas, lade of wat dan ook, kunnen wij u helpen. Je kunt Shadow Foam uiteraard bestellen in elk formaat tot 2m x 1m via onze Custom Size- service, dus als je een vierkante lade hebt, dan is dat perfect.
Maar wat als u een container met een afwijkende vorm heeft om in te passen, of radiussen op de hoeken, of als u een medium vel Shadow Foam of een Value Pack wilt kopen en deze op maat wilt knippen? Daar hebben wij een handleiding voor!

Het is heel goed mogelijk om zelf een op maat gemaakt schuiminzetstuk te maken dat in elke container past. Kijk hier voor meer informatie over hoe u dat doet. Het is niet teccy of verfijnd, maar het is iets dat iedereen zou kunnen doen, gewoon met materialen die je thuis nog hebt liggen. En het is supereffectief!
Een speciale opmerking… tijd en geduld
Als u een van onze YouTube-video's bekijkt, ziet u hoe snel wij door onze projecten zoeven. We zeggen vaak dingen als “dit kostte ons minder dan een paar uur” en dit is allemaal waar. Maar dit doen wij de hele tijd ! We hebben de technieken en processen uit het hoofd en kunnen dit vrijwel in onze slaap doen. Maar als je nieuw bent met shadowfoaming, is het de moeite waard om in het begin wat meer tijd te nemen om de beste resultaten te bereiken. De snelheid en het gemak zullen absoluut met de tijd komen, maar zoals met alles duurt het even voordat je eraan gewend bent.
Maar het is echt niet moeilijk; iedereen kan dit doen, vrijwel overal, zoals dit voorbeeld illustreert.
We kennen allemaal het oude gezegde: “twee keer meten, één keer knippen” en hetzelfde geldt hier. Met geduld en een methodische aanpak volgens onze best practices en tutorials, vliegt ook u op tijd door uw toolorganisatie.
Snijden
Het is geen toeval dat we in de meeste van onze YouTube-video's de beste en veiligste technieken voor het snijden van schuim behandelen. Het is een heel belangrijk onderdeel van het proces. Als je nog nooit met Shadow Foam hebt gewerkt, bekijk dan zeker ook deze How To-gids .

- Houd het item met één hand op zijn plaats.
- Houd met de andere hand het scalpel vast als een potlood en teken de snede helemaal rond het voorwerp af
(dwz niet helemaal afsnijden, net genoeg zodat je het silhouet van het item kunt zien) - Verwijder het item en ga terug naar je trace-snede, waarbij je de diepte in het schuim snijdt die je nodig hebt
(je kunt de lengte van het mes gebruiken als visuele referentie voor deze diepte, en als je begint met afpellen, kun je ook de lagen die je in het schuim ziet als richtlijn gebruiken) - Het is belangrijk dat je diep genoeg hebt gezaagd tot waar je de basis van het item wilt hebben, dus zorg ervoor dat de punt van je mes zo ver of zelfs iets verder reikt dan waar je de basis wilt hebben.
(hoewel je altijd weer naar binnen kunt gaan en kunt knippen nadat je een laag of twee hebt verwijderd, om zeker te zijn)
Peeling
Dit is absoluut bepalend voor hoe goed uw project wordt, hoe goed het resultaat eruit ziet en hoe gemakkelijk u het proces vindt. Deze techniek brengt je in een mum van tijd van beginner naar expert en we raden iedereen aan om zich op te frissen in dit proces voordat ze beginnen met schaduwschuimen!

- Duw uw vinger(s) in het schuim aan het ene uiteinde van het profiel van het uitgesneden item
- Ga door met je vinger(s) door het schuim te ploegen, zodat je het hoort loskomen op de plek waar je je vingers erdoorheen duwt
(laat je niet verleiden om vast te houden en te pellen alsof je een banaan schilt, zoals op de foto, hij zal gewoon afbreken en je zult opnieuw moeten gaan. Dit kost wat kracht en moeite en is opzettelijk zodat het schuim sterk genoeg is om na verloop van tijd niet uit elkaar te vallen) - Misschien wil je de lagen beetje bij beetje afpellen, dat is prima. Zodra je één laag hebt verwijderd, ga je er weer naar binnen en doe je hetzelfde opnieuw.
- De gelamineerde laagpunten van 10 mm die u in het schuim kunt zien, kunnen de moeilijkste punten zijn om af te pellen, dus voor het beste resultaat kunt u proberen om op een van de andere punten boven en onder deze punten af te pellen.
Afwerking
Testpasvorm
Wanneer u uw gereedschap in het schuim plaatst, moet het super goed passen. Maar als er nog een beetje extra moet worden gesneden rond of in het schuim om het goed of plat te laten zitten, dan is dit een goed moment om er weer mee aan de slag te gaan. Sommige items met een ongelijke basis hebben op sommige gebieden wat meer snit nodig dan op andere
Het afvlakken van de basis
Er wordt ons vaak gevraagd hoe u een vlakkere basis op uw uitgesneden gebied kunt krijgen. Dit komt deels door het gebruik van de beste peelingtechniek, zoals we hierboven aanbevelen. Maar dit is natuurlijk schuim, en het materiaal is van nature hobbelig. Maak je dus geen zorgen als de basis van je geschilde gebied niet helemaal vlak is.
Maar als je net als wij perfectionistisch bent, dan zijn er manieren om een zo vlak mogelijk resultaat te bereiken. Wanneer u met de hand snijdt, kunt u dit doen door eventuele "klontjes" weg te scheren terwijl uw scalpelmes er horizontaal tegenover staat en ze gewoon weg te wrikken.
We hebben nu echter ook een hele reeks gereedschappen en technieken voor het gladmaken van schuim die we met u kunnen delen, dus bekijk hier de mogelijkheden voor het gladmaken!
Maatwerk
Je hebt misschien gezien dat we ons logo vaak in onze merken hebben geknipt, maar veel andere mensen hebben hetzelfde zelf kunnen doen door branding, logo's, namen of initialen toe te voegen aan hun schuimorganizers. Zoals je uit deze selectie hieronder zult zien, kan dit er super effectief uitzien.
Al het schuimsnijden dat we doen is met de hand, en ook deze zijn op dezelfde manier gemaakt, zodat je echt geweldige resultaten kunt bereiken. Hier kun je zien hoe we een van onze eigen gereedschapsmuren personaliseren, zodat je hetzelfde kunt repliceren en uitproberen.

Neem contact op
We hopen dat deze gids en alle videolinks u helpen bij uw missie om georganiseerde perfectie te bereiken! Maar als er nog iets is waarmee we u kunnen helpen, zoals altijd, neem dan gerust contact met ons op .